Why a Reliable Chemical Defoamer Is Important for Ensuring Operational Efficiency
Why a Reliable Chemical Defoamer Is Important for Ensuring Operational Efficiency
Blog Article
Checking Out the Conveniences of a Chemical Defoamer in Manufacturing and Manufacturing
The assimilation of chemical defoamers in production and production procedures provides a critical advantage by resolving one of the persistent obstacles in industrial procedures: foam control. Chemical Defoamer. Understanding the nuances of numerous kinds of defoamers and their specific applications can expose their substantial impact on functional efficiency and product high quality. As manufacturers aim to maximize procedures and enhance client satisfaction, the function of chemical defoamers becomes progressively essential. Yet, the concern stays: just how do these substances essentially modify the landscape of manufacturing performance and cost-effectiveness?
Importance of Foam Control
While the presence of foam in manufacturing processes can sometimes seem harmless, effective foam control is essential for enhancing operational effectiveness and product quality. Foam can hinder various phases of manufacturing, leading to ineffectiveness that may boost costs and expand handling times. In markets such as food and beverage, pharmaceuticals, and chemicals, uncontrolled foam can block tools, interfere with automated systems, and inevitably cause product disparities.

Executing reliable foam control strategies not only improves efficiency yet additionally sustains regulatory compliance in industries where foam can result in ecological worries. By making use of chemical defoamers, suppliers can mitigate these challenges, guaranteeing smoother operations and higher-quality final result. Eventually, prioritizing foam control is a necessary facet of production that can generate substantial advantages in regards to safety, product, and efficiency reliability.
Sorts Of Chemical Defoamers
What sorts of chemical defoamers are offered for producing processes, and how do they differ in application? Chemical defoamers can be classified right into three main types: silicone-based, natural, and not natural defoamers. - Chemical Defoamer

Organic defoamers, typically originated from all-natural oils or fats, are efficient in an array of applications, including food and beverage production. They are commonly preferred for their reduced poisoning and environmental impact, making sure conformity with sector regulations.

Each kind of defoamer offers unique purposes based upon the chemical composition and the details requirements of the production process, allowing makers to choose one of the most appropriate option for their certain demands.
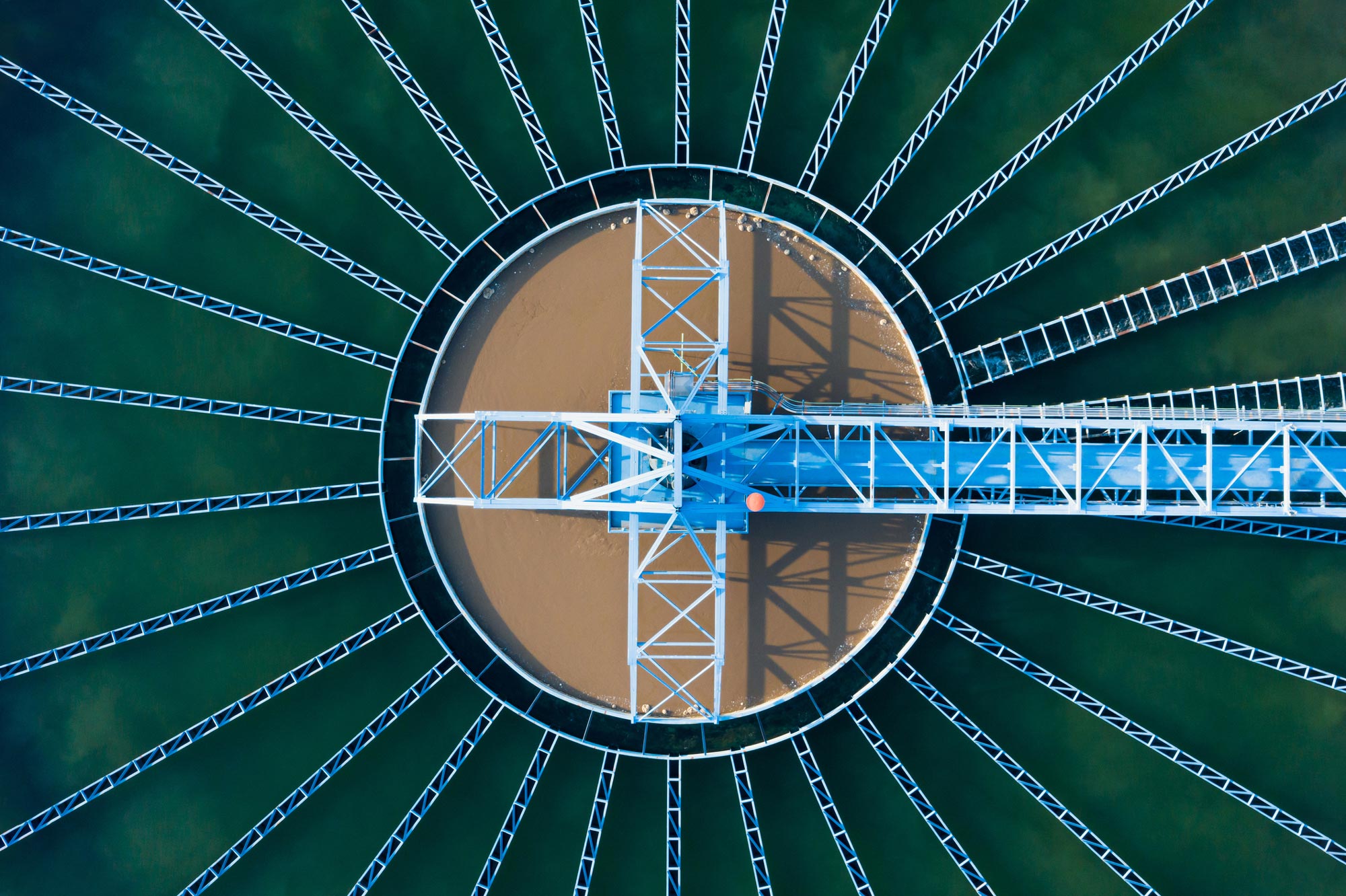
Benefits in Manufacturing Performance
Chemical defoamers play a vital role in boosting manufacturing performance by effectively managing foam generation during different procedures. Foam can hinder manufacturing prices, interrupt tools operation, and cause pricey downtime. By incorporating chemical defoamers, makers can mitigate these problems, making certain smoother workflow and boosted total productivity.
Using chemical defoamers aids optimize the operational efficiency of tools such as activators, pumps, and mixers. With decreased foam, these equipments can run at their intended capability, lessening the threat of overflow and enabling consistent processing. This leads to far better source utilization and higher throughput.
Furthermore, chemical defoamers help with faster processing times by decreasing the time required for foam elimination. This velocity can dramatically impact production schedules, allowing producers to satisfy client need extra properly. Additionally, making use of defoamers contributes to decrease energy usage, as equipment runs much more effectively with minimized foam disturbance.
Influence On Product High Quality
Foam control is not only vital for preserving effectiveness in producing processes but likewise plays a considerable role in ensuring item top quality. Too much foam can present air right into formulas, resulting in disparities in the final product. This can show up as issues such as gaps, unequal structures, or substandard finishes, which threaten the desired you could try here high quality and performance of the product.
In addition, foam can prevent the homogeneity of blends, leading to uneven circulation of energetic ingredients. In industries such as coatings, cosmetics, and food manufacturing, this can cause variations in shade, preference, and overall effectiveness. By making use of a chemical defoamer, makers can reduce these threats, making sure that products fulfill rigid high quality specifications.
Furthermore, regulating foam can improve the security of solutions and suspensions, which is important for guaranteeing shelf-life and consumer complete satisfaction. With enhanced product consistency and minimized flaws, makers can attain higher criteria of quality control, eventually leading to raised customer trust fund and brand commitment.
Cost-Effectiveness and ROI
Effective foam control not just enhances item quality however additionally contributes dramatically to the general cost-effectiveness of making processes. Making use of chemical defoamers minimizes foam-related concerns, which can otherwise cause production delays, tools useful reference malfunctions, and boosted power intake. By lowering foam, makers can optimize their procedures, bring about higher throughput and effectiveness.
Buying chemical defoamers can produce a substantial roi (ROI) The preliminary prices connected with these additives are frequently offset imp source by the cost savings understood from decreased downtime and improved product return. In addition, enhanced item top quality can decrease waste and revamp prices, even more bolstering economic efficiency.
Furthermore, efficient foam control can lead to reduced water and energy use, adding to reduced operational costs. This is specifically crucial in industries where source effectiveness is paramount. By incorporating chemical defoamers right into their processes, makers can accomplish lasting financial savings while maintaining competitive prices in the industry.
Final Thought
To conclude, the combination of chemical defoamers in production and manufacturing procedures is essential for maximizing operational effectiveness and improving product quality. Reliable foam control contributes to improved tools performance, lowered processing times, and decreased downtime, inevitably causing substantial expense financial savings. Furthermore, constant item formulations foster consumer satisfaction and brand commitment. The advantages offered by chemical defoamers not just sustain governing conformity however additionally supply an one-upmanship in the production landscape.
The assimilation of chemical defoamers in manufacturing and production processes provides a critical advantage by resolving one of the persistent challenges in commercial procedures: foam control.While the visibility of foam in manufacturing processes can sometimes seem harmless, efficient foam control is important for optimizing functional effectiveness and product quality.Chemical defoamers play an important role in improving manufacturing performance by properly managing foam generation throughout various processes.Moreover, chemical defoamers facilitate faster handling times by decreasing the time required for foam elimination. Additionally, the usage of defoamers adds to reduce energy intake, as equipment runs a lot more successfully with reduced foam interference.
Report this page